1. Color Masterbatches
Color masterbatches provide vibrant and consistent coloration to plastic products without the need for additional steps or processes.
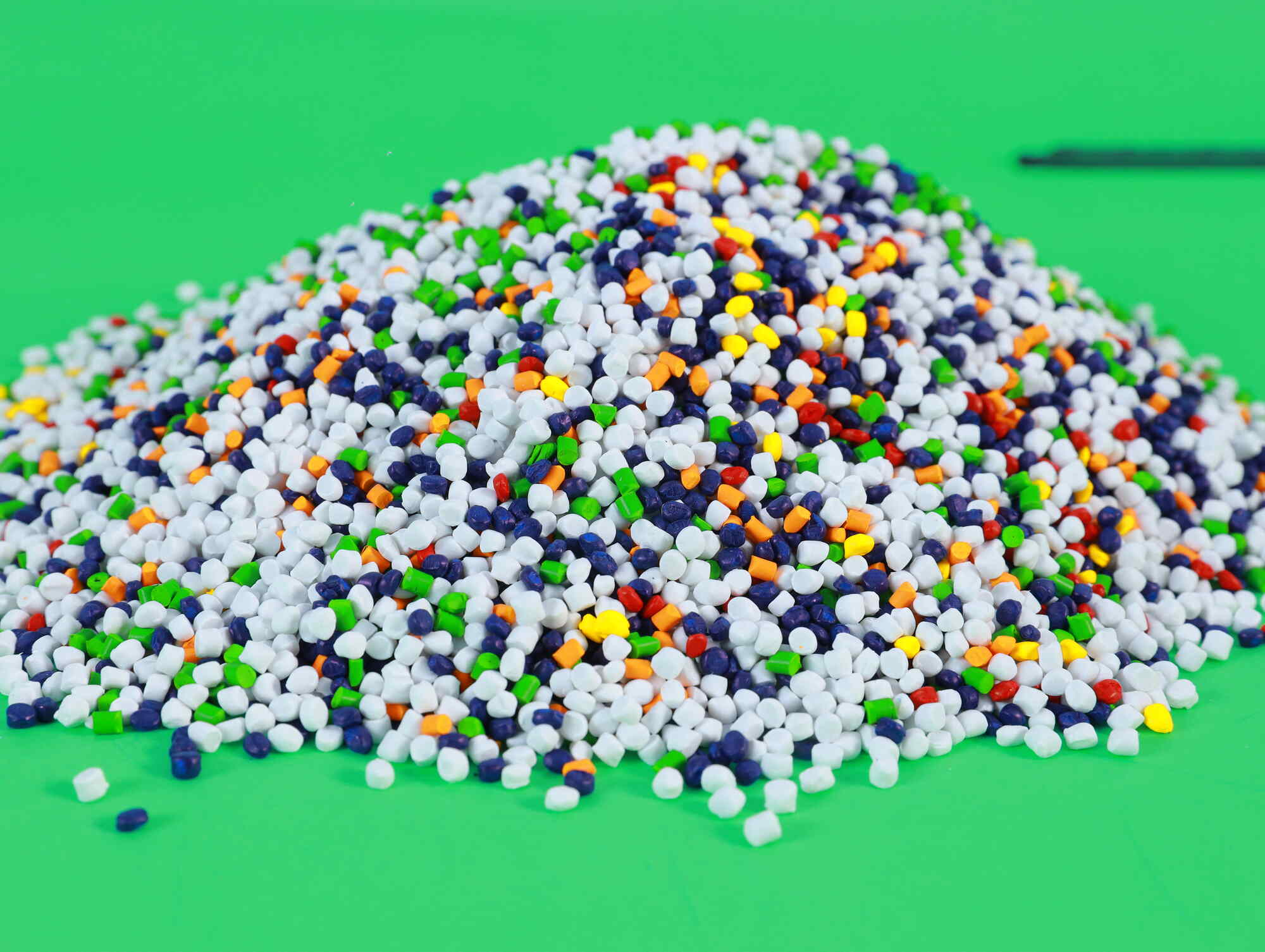
Applications
- Packaging: Used extensively in packaging materials to create visually appealing and brand-specific colors.
- Consumer Goods: Essential for household items, toys, … to make them attractive and marketable.
- Automotive: Utilized in the interior and exterior parts of vehicles to provide durable and vibrant colors.
2. White and Black Masterbatches
White and black masterbatches are specialized forms of color masterbatches but with unique properties that make them indispensable in various applications.

Applications
- White Masterbatch: Contains titanium dioxide, providing excellent opacity and brightness. Used in products such as packaging, household item, blow molding products.
- Black Masterbatch: Contains carbon black, offering UV protection and conductive properties. Ideal for automotive parts, agricultural films, and pipes.
3. Filler Masterbatches
Filler masterbatches are used to modify the density, improve the mechanical properties, and reduce the production costs of plastic products. They typically contain materials such as calcium carbonate, talc, or barium sulfate.

Applications
- Packaging: Enhance the strength and rigidity of plastic films and containers.
- Injection & Extrusion: Improve the durability and performance of household items.
- Blow Molding: Increase the rigidity of cans, bottles, jars,…
- Woven: Improve in impact strength, stiffness, barrier properties, and print quality
- Non woven: Increases the strength of the material, create softness like cotton
4. Additive Masterbatches
Additive masterbatches are designed to improve the physical and chemical properties of plastics. They can offer benefits such as UV resistance, antiblock, anti-static properties, and more.

Applications
- UV Stabilizers: Protect plastics from degradation caused by ultraviolet light. Widely used in outdoor applications such as garden furniture and agricultural films.
- Anti-Block Additives: reducing surface contact between film layers, thereby minimizing the occurrence of blocking in blown film manufacturing.
- Anti-Static Additives: Reduce the buildup of static electricity, crucial for electronic packaging and components.
- Desiccant Additives: Absorb moisture during the manufacturing process, preventing defects such as bubbles, voids, and hydrolysis, applied in production of mobile chargers, power sockets, and electronic components.
- Optical Brightener Additives: Enhance appearance, making plastics look brighter and more vibrant, applied in cosmetic packaging, household items, and high-visibility safety equipment
Conclusion
Selecting the right masterbatch is crucial for achieving the desired properties and performance in plastic products. Color, additive, filler, white, black, and special effect masterbatches each offer unique benefits and are suited for specific applications within the plastic industry. By understanding the role and advantages of each type, manufacturers can optimize their processes and produce high-quality, functional, and visually appealing plastic products.

POLYINNOTECH.,JSC is a Vietnamese manufacturer specializing in masterbatch products. Our extensive range includes filler masterbatch, white masterbatch, black masterbatch, color masterbatch, additives, and engineering compounds. With a global presence and commitment to quality, POLYINNOTECH is a trusted name in the industry.